PRODUCTS CENTER
MAIN PRODUCTS
We always takes customer satisfaction as its service goal and provides customers with integrated services.
CONTACT USABOUT US
Shandong Wanguo Metal Products Co., Ltd.
Shandong Wanguo Metal Products Co., LTD was founded in 2011. We are a manufacturer of metal products. Company production: steel pipe, steel coil, steel plate, steel rod. Material: stainless steel, carbon steel, galvanized steel We provide polishing/bending/cutting/secondary machining services. The company always takes customer satisfaction as the service goal and provides integrated services for customers.
MORE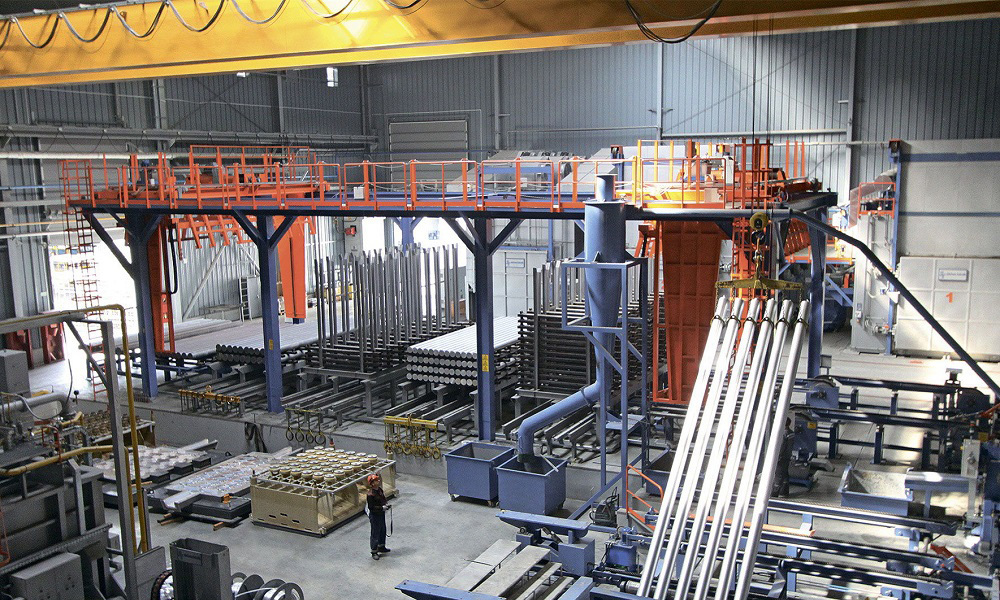
Thank you for your message, we will contact you at the first time!
NEWS CENTER
07-21
05-16
WANGUO STEEL
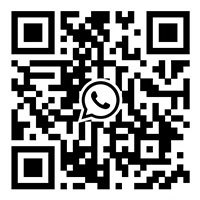
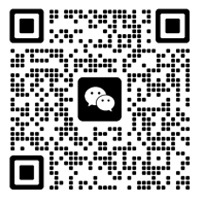
Webpage Copyright © 2022 Shandong Wanguo Metal Products Co., Ltd.
Powered by : WWW.300.CN JINAN2 SEO